The Application of a Volumetric Doser in the Plastic Industry
Application Solution of Measuring Volumetric Doser in Plastic Processing Industry
The metrological color masterbatch provides an efficient and precise color control method in the plastic processing industry, and is a key equipment for achieving high-quality plastic product production. The following will provide a detailed introduction to its application solutions to ensure that plastic processing enterprises can fully utilize the potential of this equipment, improve product quality and production efficiency.
Determine application requirements
(1) Material type and production volume: Select the appropriate model of volumetric doser based on the type of raw materials and production scale to ensure that it can meet production needs.
(2) Color and additive requirements: Determine the required color masterbatch functions based on the product’s color requirements and the types of additives, such as whether multi-component functionality is needed to support parallel input of multiple colors or additives.
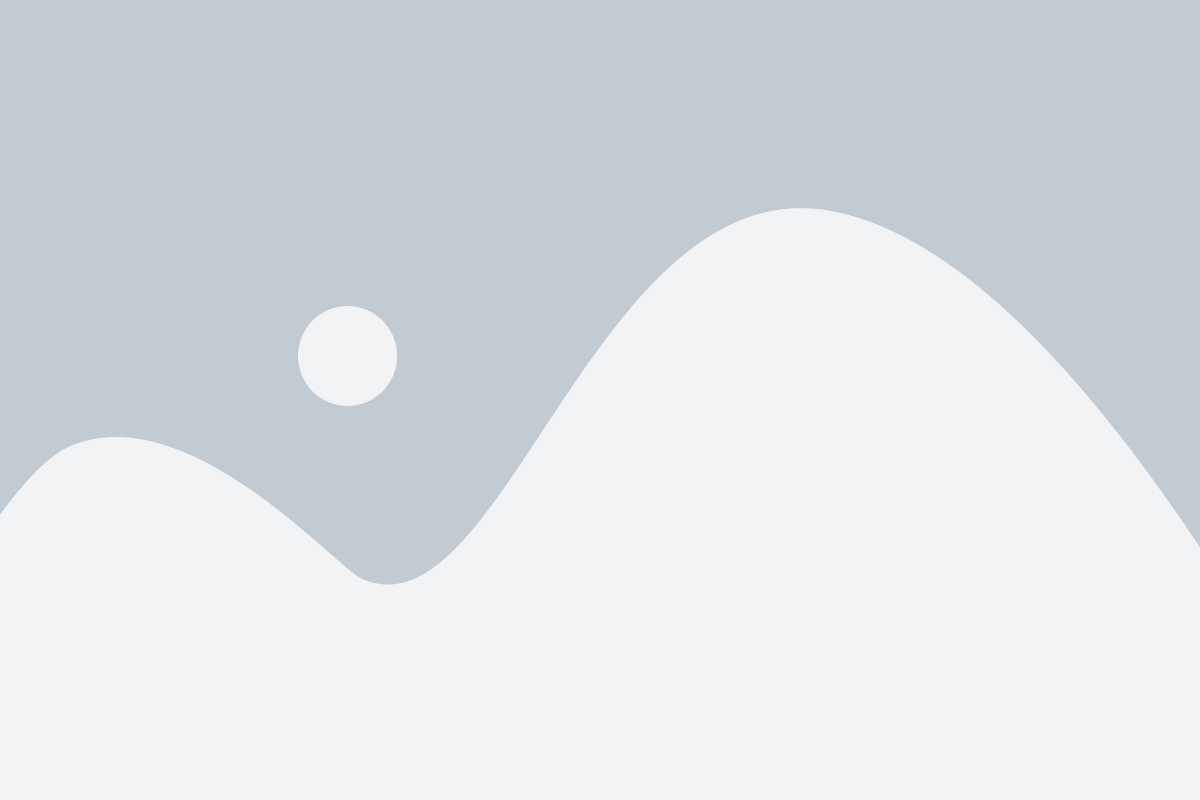
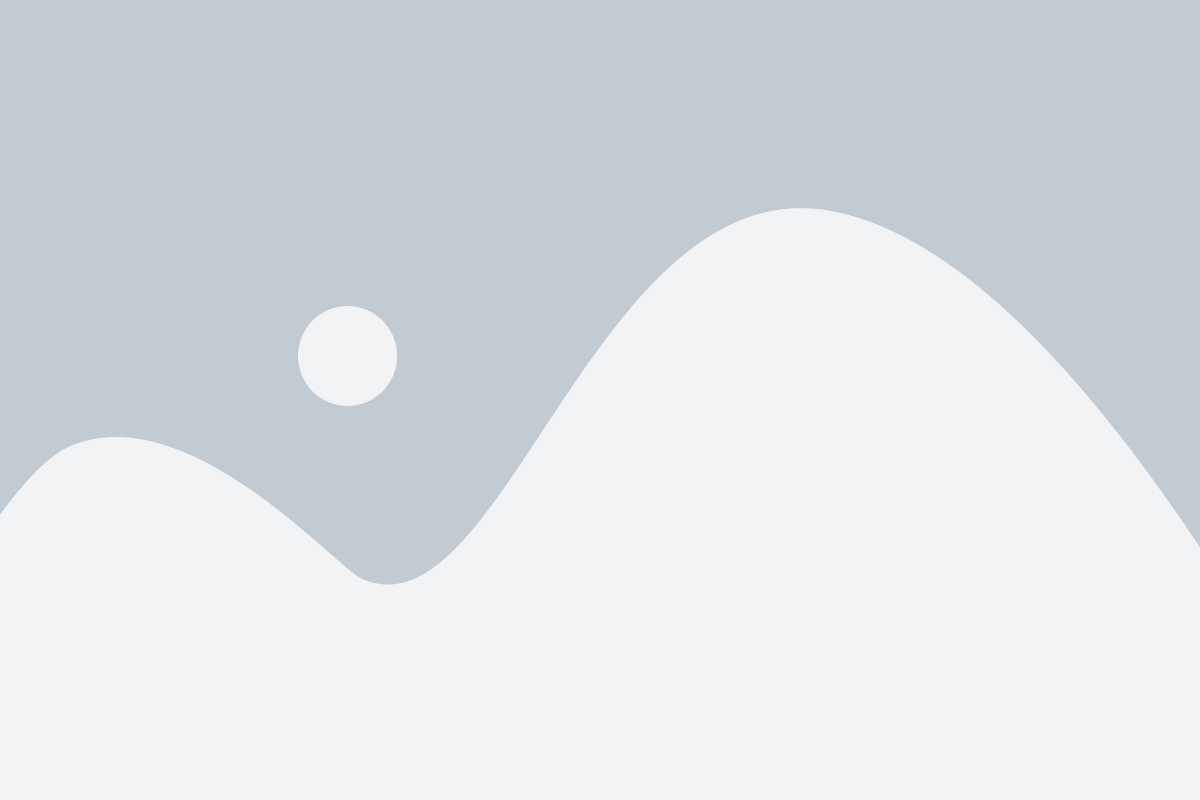
Equipment configuration and installation
(1) Correct configuration: Ensure that the volumetric doser has the necessary measuring and mixing capabilities, select suitable screw diameters and production ranges to meet different production needs. Adopting PLC control and color touch screen for easy operation and setting.
(2) Integration into the production line: The volumetric doser needs to be seamlessly integrated with existing equipment such as injection molding machines, extruders, or blow molding machines, and can operate automatically through synchronous signals without pre dyeing materials, improving production efficiency and product performance.
Process optimization
(1) Mixing uniformity: By utilizing the precise metering and mixing function of the volumetric doser, it ensures that the color masterbatch and raw materials are mixed in the predetermined proportion, avoiding color differences, stripes or spots in the product, and ensuring the consistency and quality stability of the product color.
(2) Temperature and back pressure control: Moderately adjust the temperature range of the masterbatch mixing chamber and apply an appropriate amount of back pressure on the masterbatch to optimize the dispersion and mixing effect of the pigment. At the same time, pay attention to adjusting the injection speed and mold temperature to improve product quality.
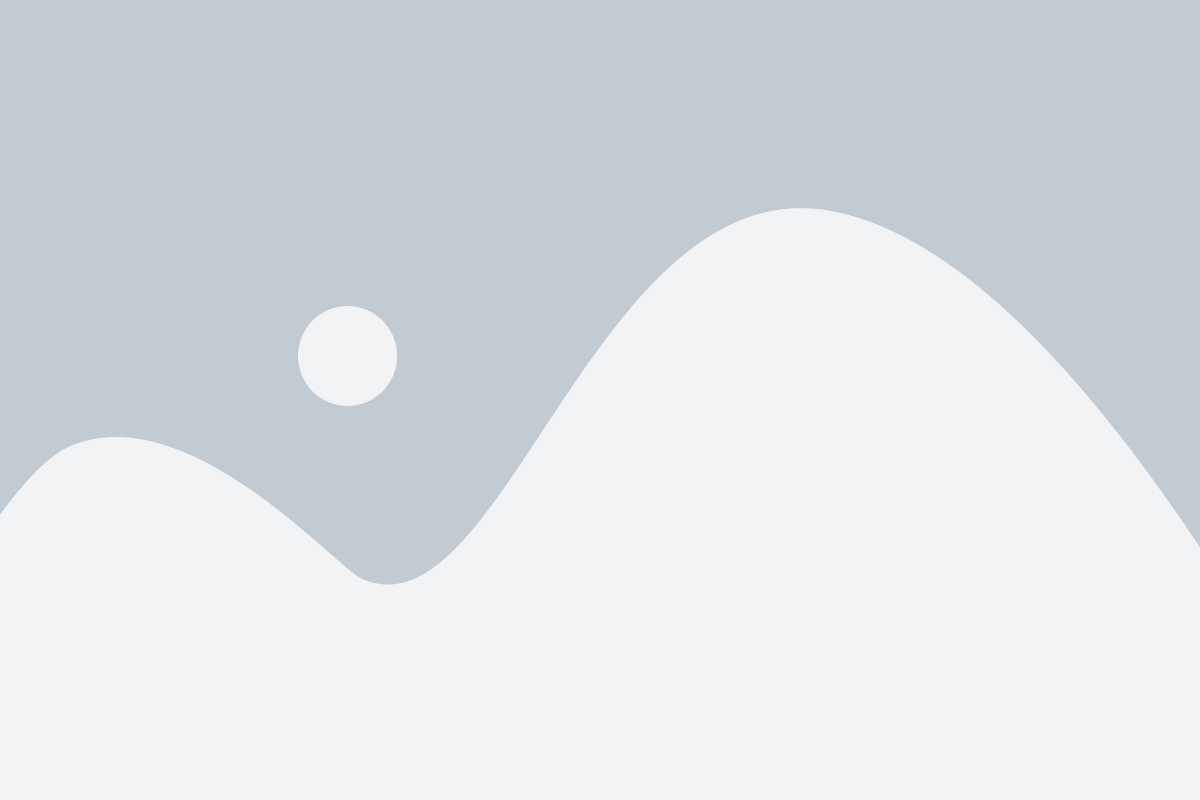
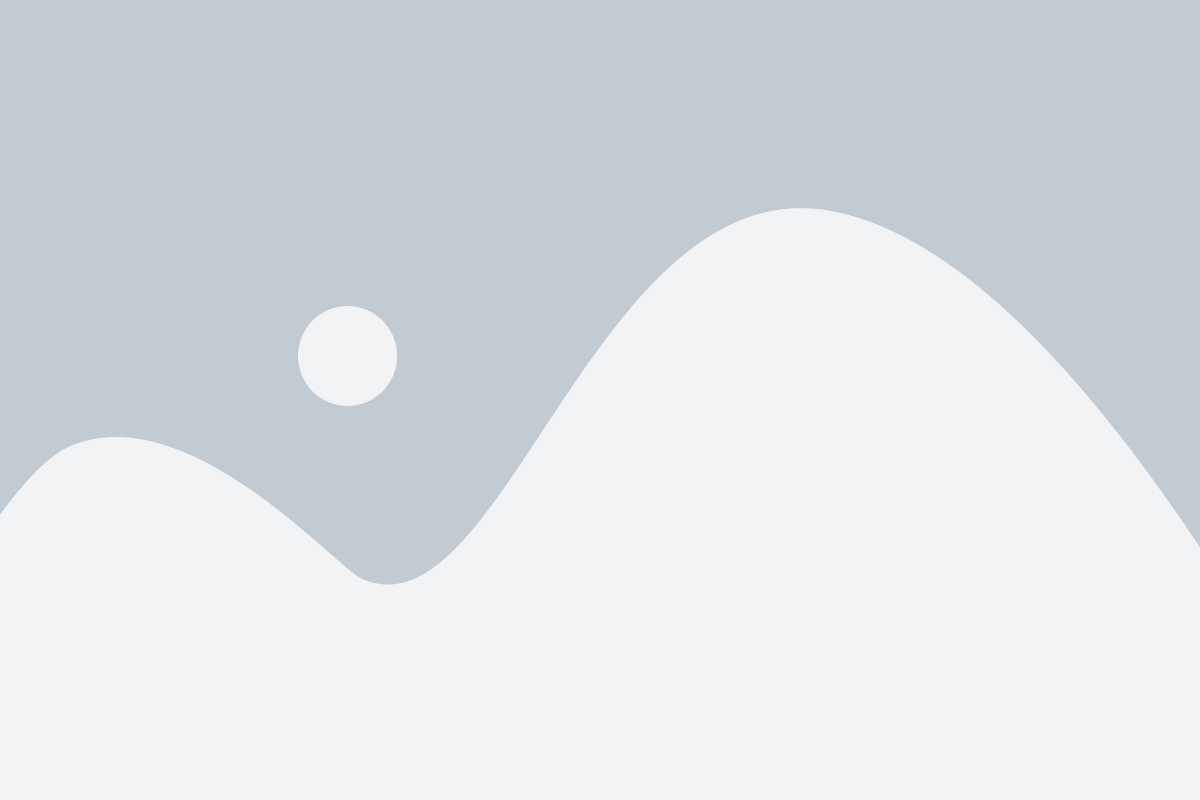
Automation and control systems
(1) Automation level: Based on the automation requirements of the production line, select an appropriate level of automation control system, including functions such as automatic detection and adjustment of the amount of color masterbatch added, reducing manual intervention, improving production efficiency and product consistency.
(2) Feedback and data analysis: Establish a feedback mechanism in the production process, collect and analyze production data to optimize the production process, improve color accuracy and reproducibility, and reduce scrap rates.
Training and maintenance
(1) Operation training: Provide sufficient training for operators to ensure that they understand the working principles and operating procedures of the equipment, and can proficiently carry out daily operations and maintenance.
(2) Continuous maintenance: Develop regular maintenance plans, replace worn parts in a timely manner, maintain the best working condition of equipment, and prevent production interruptions and quality issues.
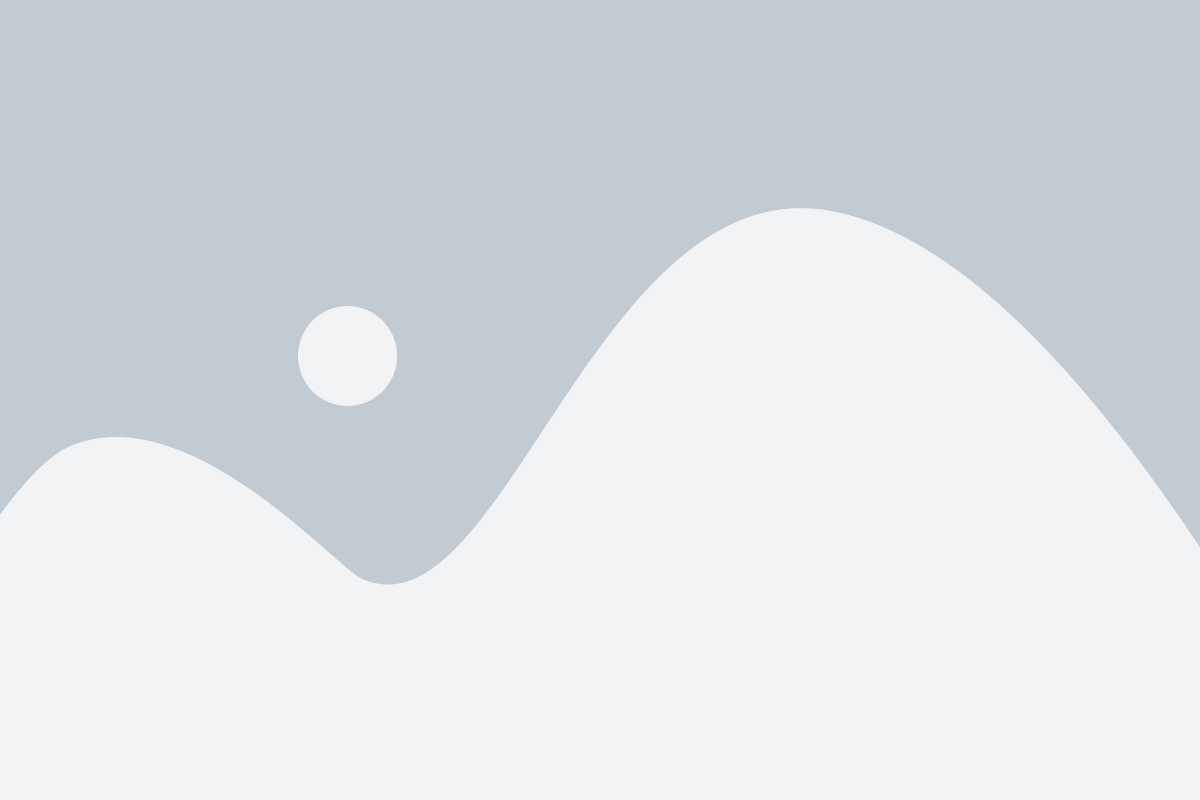
In summary, the volumetric doser provides an efficient and reliable solution for the plastic processing industry, significantly improving product quality and production efficiency through precise measurement and mixing. The correct equipment selection, optimized production process, strict operation training, and meticulous maintenance are the key to ensuring the maximum efficiency of the volumetric doser.