The Application of a Centrifugal Deoiler in the Plastic Industry
Application Solutions For The Centrifugal Deoiler Industry
In industrial production, the application of cutting fluids and metalworking oils is very common, and they play a key role in lubrication, cooling, and rust prevention. However, with the increasingly strict environmental regulations and the increasing demand for resource conservation, higher requirements have been put forward for the recycling and reuse of cutting fluids and metalworking oils. The application solution of Centrifugal Deoiler in this industry not only effectively addresses these challenges, but also brings dual improvements in economic and environmental benefits to enterprises. The following is an introduction to the application solutions of the degreaser in rapidly degreasing and dehydrating cutting chips, enabling the centralized recycling and reuse of metal cutting oil and emulsion:
Efficient oil and liquid removal technology
(1) Centrifugal force separation: The degreaser uses centrifugal force to generate strong centrifugal force through high-speed rotation, effectively separating oil and grease from metal shavings. This technology can not only quickly remove the grease on the surface of metal shavings, but also ensure high dryness without damaging the metal shavings themselves.
(2) Basket design: The stainless steel wedge-shaped gap screen used in the equipment has the characteristics of being difficult to block and having high separation efficiency, greatly reducing the drying time of chips and improving the oil removal efficiency.
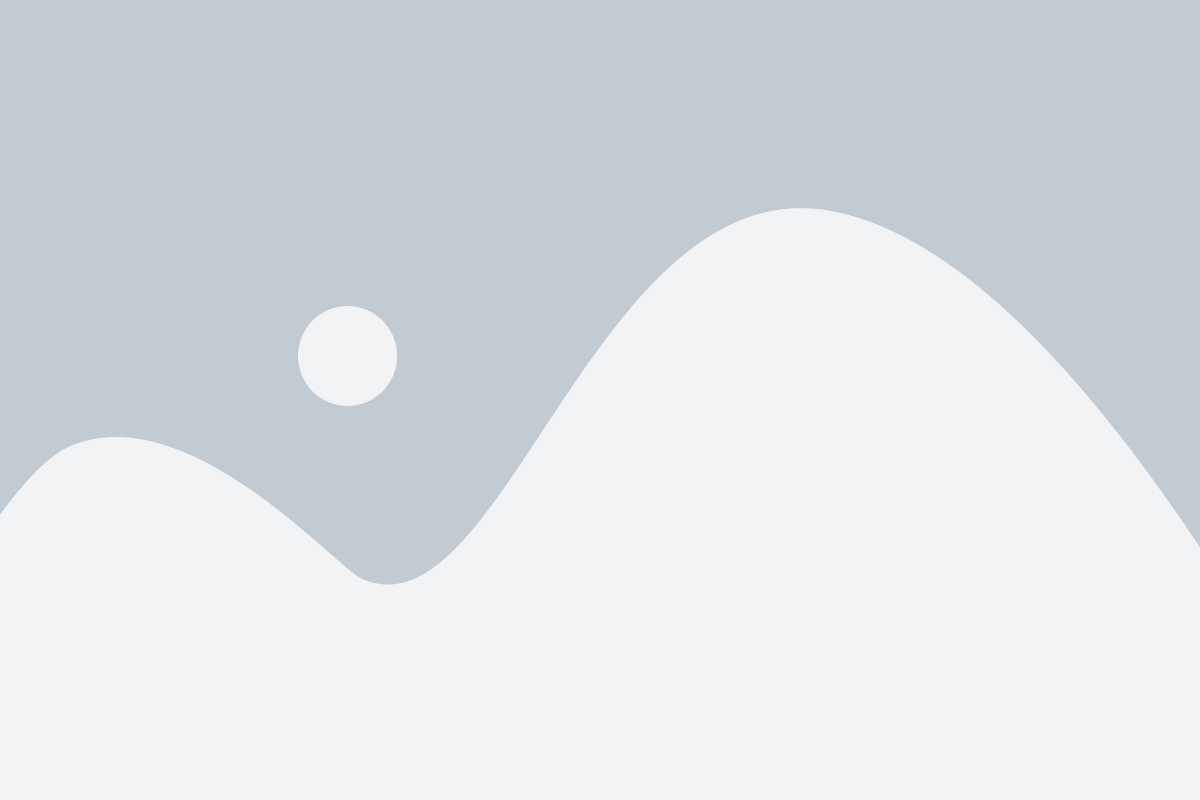
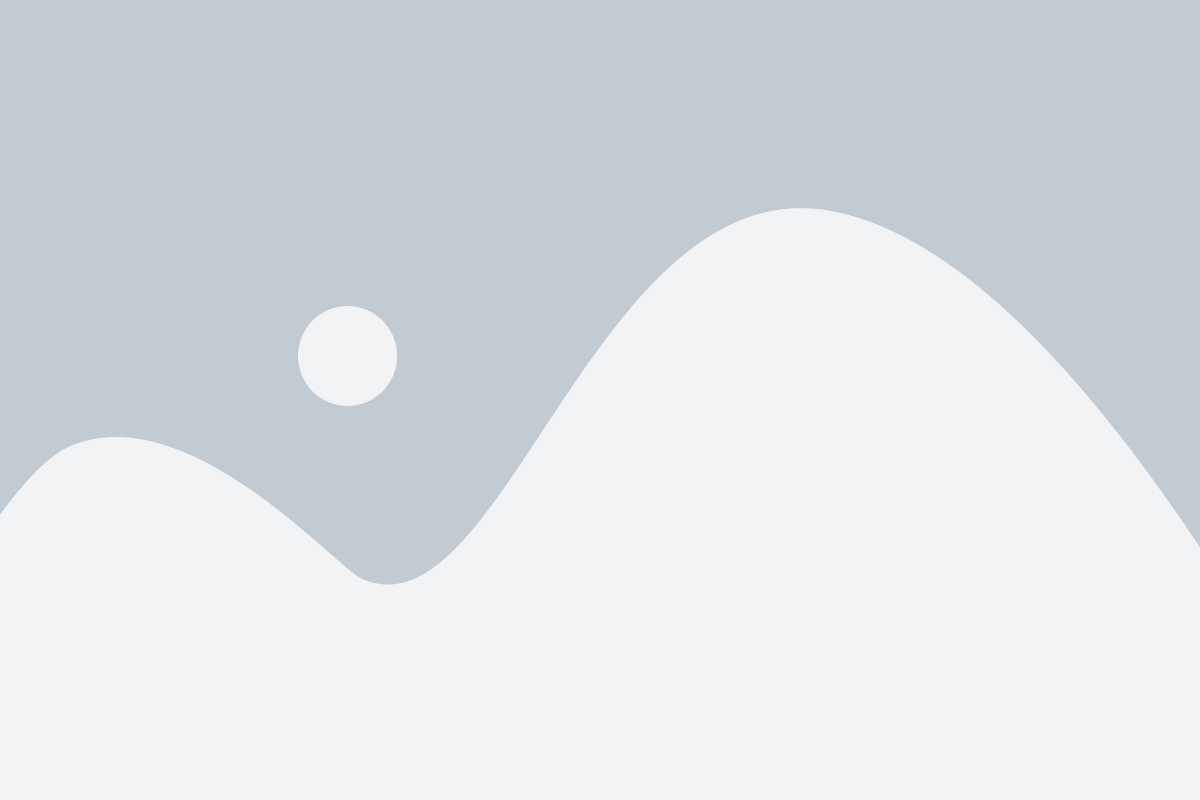
Centralized recycling and reuse system
(1) Oil collection bin and automatic flushing: The oil collection bin with automatic flushing function effectively solves the problem of oil outlet blockage caused by small chips, ensuring that cutting oil and emulsion can smoothly enter the collection container for subsequent centralized processing and reuse.
(2) Reuse mechanism: The degreaser not only separates oil from metal shavings, but also designs collection channels and oil outlets, allowing the removed oil to be centrally processed for use in other production processes or reused after purification, achieving resource recycling.
Automation and intelligent control system
(1) PLC control: Using a PLC control system, users can adjust the oil removal time and speed according to different types of metal shavings and processing requirements, achieving simplified and precise operation.
(2) Seismic isolation technology and sensors: Through the application of seismic isolators and vibration sensors, the oil separator can automatically adjust its working state, ensuring that the equipment operates at its optimal state while reducing the impact on the equipment and working environment.
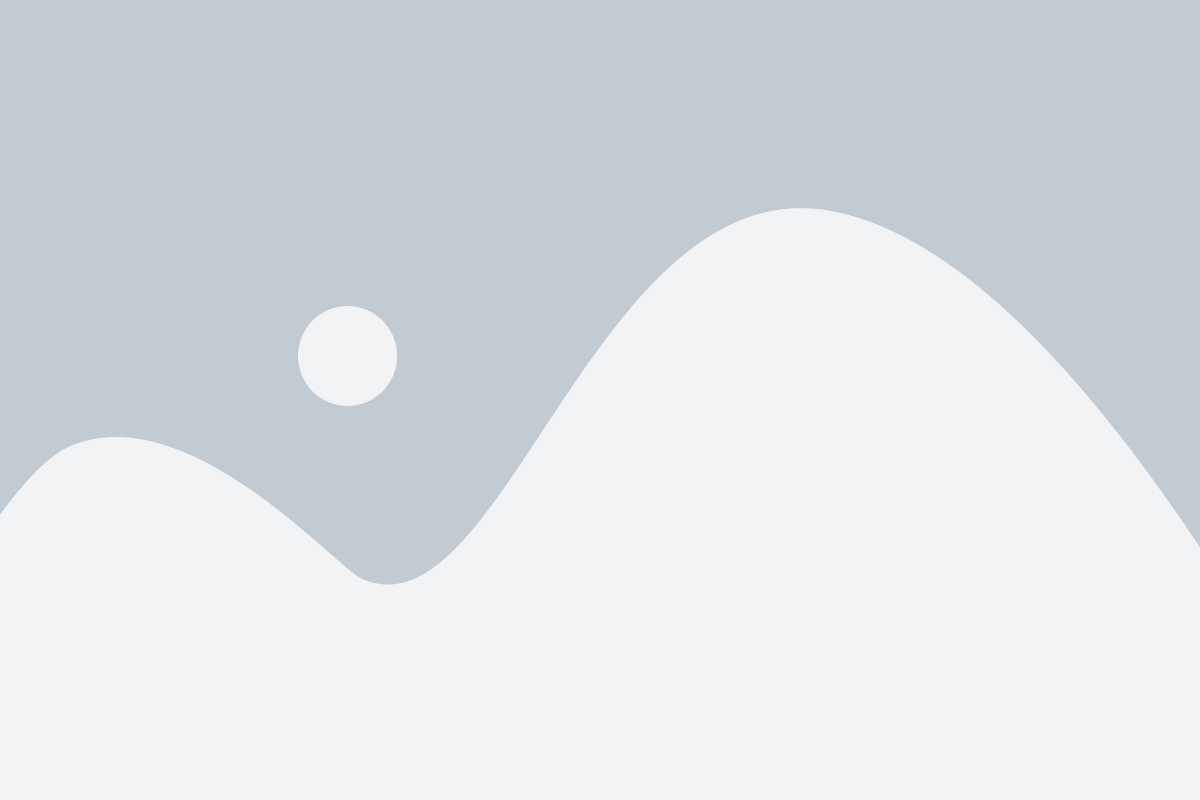
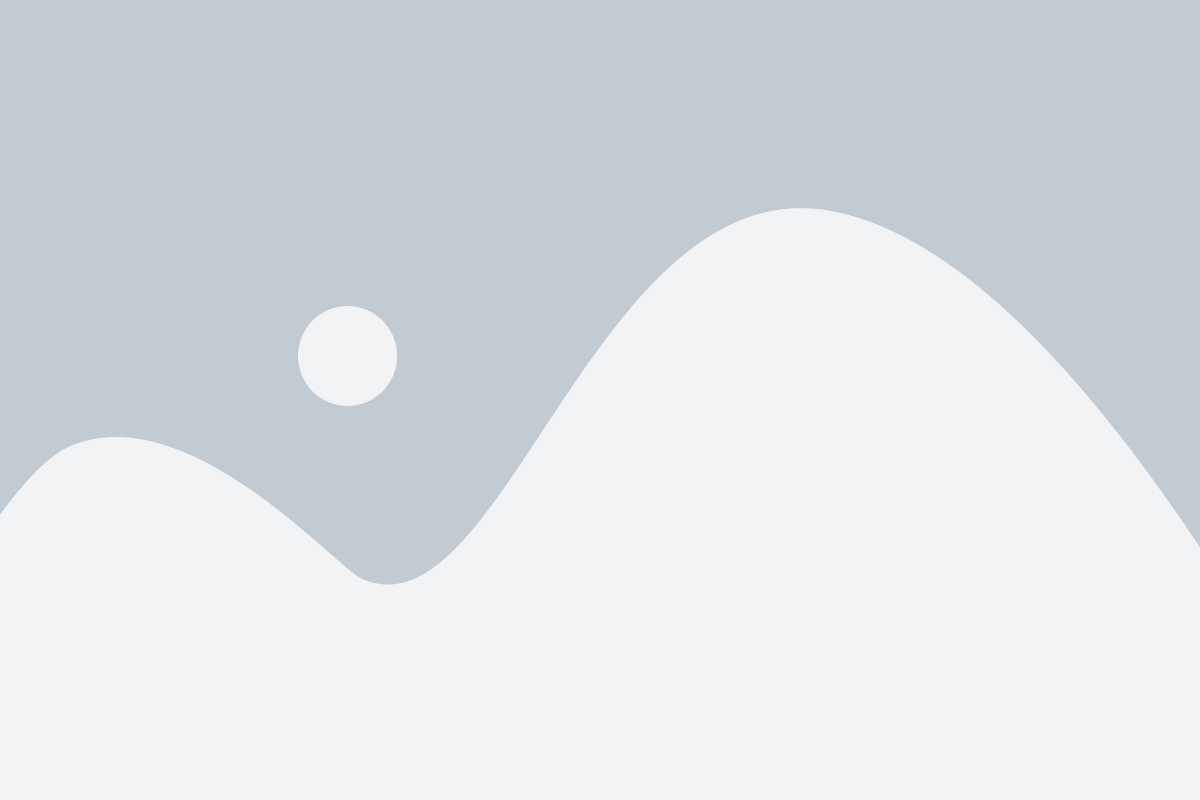
Dual improvement of environmental protection and economic benefits
(1) Reduce waste emissions: Effectively separate metal shavings from grease, reduce factory waste emissions, comply with today’s strict environmental regulations, and avoid possible environmental penalties.
(2) Improving furnace efficiency and sales value: Dry metal shavings furnaces have higher efficiency, enhance the reuse value of metals, increase additional income for enterprises, and achieve cost savings and increased benefits.
Wide range of applications
(1) Applicability of different metal processing industries: The degreaser is suitable for various metal processing industries such as iron chips, aluminum chips, copper chips, etc., and can play its role in machine tool processing workshops such as lathes, milling machines, and drilling machines.
(2) Hazardous waste disposal: According to the National Hazardous Waste List (2021 edition), metal shavings contaminated with hazardous waste such as chip fluid and waste mineral oil are classified as hazardous waste. The degreasing function significantly reduces the environmental pollution caused by oil pollution and helps enterprises pass environmental inspections smoothly.
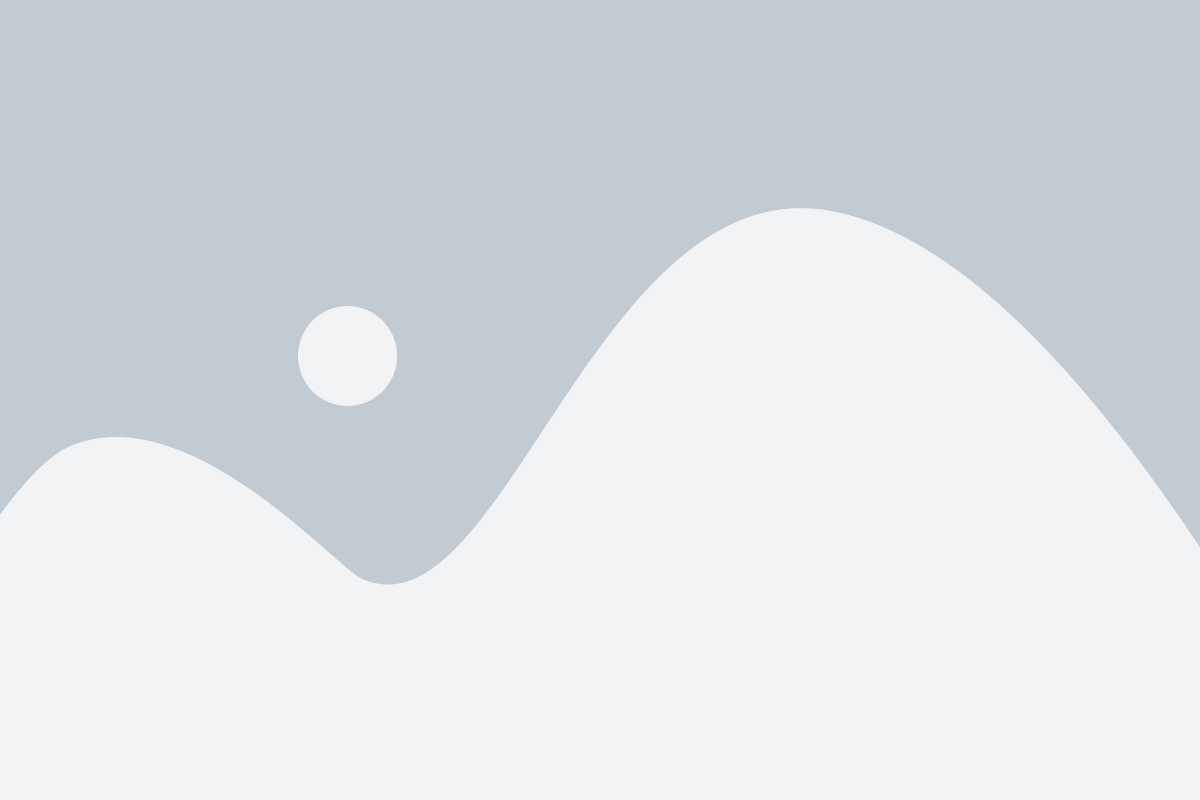
In short, in the metal processing industry, the degreaser not only solves the environmental pain points caused by cutting chips, but also brings significant environmental and economic benefits to enterprises through efficient degreasing and dehydration technology, centralized recycling and reuse systems, automation and intelligent control systems, and a wide range of applications. With the continuous advancement of technology and the increase in market demand, Centrifugal Deoiler will continue to develop, providing efficient and environmentally friendly solutions for more industries.